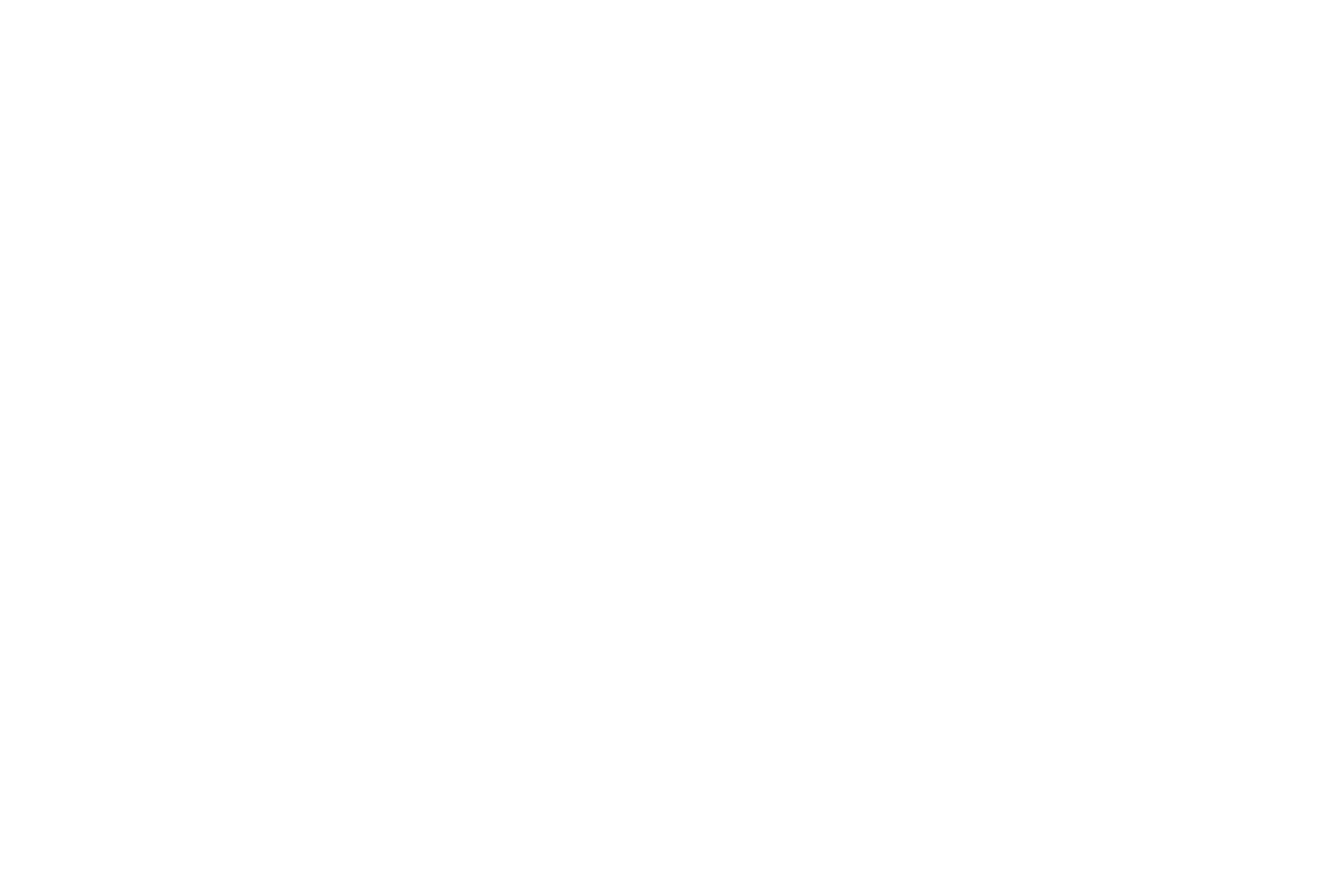
Dams work not only by storing water until it’s needed, but by moving it from one place to another. When you move it in a way that also captures the kinetic energy of the water, you can transform that energy into electricity. When you build a dam for hydroelectric purposes, it’s more than a cement pond: you also install turbines or propellers turned by the weight of the water to create electricity. As you can imagine, the equipment is huge, and even a small part can contribute to a huge loss.
The 130-foot diameter propeller that turns at the bottom of a dam in Argentina once needed regular servicing because of the 116 nuts that, with rotation and pressure, would work their way loose and compromise the functioning of the propeller. When that happens, you don’t just send in a guy with a big crescent wrench—you have to drain the entire lake! In this particular place, the lake took a year and a half to refill, causing all sorts of problems with water supply and power production. When you have regular down times of eighteen months, you take some time to think about maintenance and prevention before you build another dam.
In 1992, when the dam needed reconstruction, the hydro company contacted us to make locking nuts to replace the old ones, which had continually failed them. We did, and we haven’t heard from them again. The problem with making a product that works 100% of the time is that your customers don’t need to buy another one!